Manufacturing wind turbine components presents significant challenges in achieving precise dimensions and strength. As industry experts, we understand the complexities fabricators face in component production.
Maintaining quality while scaling production creates unique pressures in wind turbine manufacturing. Having worked with various fabricators, we recognize their need for advanced technology. Plate bending machines provide the precision required for modern tower production.
According to a report, the wind power market will reach USD 262.20 billion by 2030. Manufacturers need reliable solutions to meet this growing demand.
This blog examines how plate-bending technology transforms wind tower manufacturing. Readers will discover key processes, challenges, and future developments in production.
The Basics of Wind Turbine Construction
Wind turbine construction involves complex engineering processes that transform raw materials into sustainable energy solutions. The manufacturing requires specialized equipment and precise techniques to create components that withstand environmental forces.
The assembly process begins with the foundation, followed by the tower sections and nacelle. Using a sheet metal cone rolling machine, manufacturers can achieve the slightly conical shapes required for tower stability.
Key components in wind turbine construction:
Steel plates form the cylindrical tower sections through precise rolling and welding procedures
The nacelle houses crucial components like the gearbox, generator, and control systems
Rotor blades utilize composite materials for optimal aerodynamic performance and durability
Foundation sections provide critical support for the entire structure
Each fabricated section undergoes rigorous quality control testing. Modern manufacturing facilities employ advanced measurement systems for verification.
The manufacturing process requires specialized equipment for handling massive components. Precise tolerances must be maintained throughout the production cycle.
Each component requires specific manufacturing processes to meet strict industry standards and specifications.
Plate Bending Machines: The Backbone of Turbine Tower Production

Metal fabrication in the energy sector requires sophisticated manufacturing processes to create robust tower components. Specialized equipment transforms flat metal plates into cylindrical and conical sections for wind turbine towers.
The process begins when operators use plate-bending machines to form large metal sheets into curved sections. These sections undergo precise shaping to ensure proper structural integrity during wind turbine manufacturing.
The how to use bending machine procedures involve several key steps:
Operators align the metal plate using hydraulic side arms for accurate positioning
The plate undergoes initial pre-bending to establish the correct curvature angle
Continuous rolling creates uniform cylindrical or conical shapes with specific diameters
The final bending process requires careful monitoring to maintain dimensional accuracy and material thickness consistency. Each section must meet strict quality standards to ensure tower stability.
During plate rolling, the machine's top roll applies controlled pressure while side rolls support the material. This three-point contact system ensures uniform bending throughout the process.
Modern plate rolling systems incorporate automated controls and positioning systems. These features help maintain precise angles during the conical rolling process.
Quality control inspectors verify measurements at multiple stages of production. This ensures each tower section meets dimensional specifications before assembly begins.
The entire process requires skilled operators who understand material behavior and machine capabilities. Their expertise ensures consistent production of high-quality wind turbine components.
How Plate Bending Machines Are Used in Manufacturing of Wind Turbine Components?
Modern manufacturing processes have transformed wind turbine production into a precision-driven industry. Advanced machinery enables fabricators to create components that meet strict engineering requirements.
Tower Section Fabrication
The fabrication process starts with heavy steel plates being formed into cylindrical sections. A sheet-bending machine shapes these massive components according to specific requirements.
Key aspects include:
Processing plates up to 140mm thick for offshore applications
Creating sections with diameters ranging from 3 to 7.5 meters
Precision Bending
Automated control systems ensure exact measurements during the bending process for sections. The machines maintain consistent pressure through sophisticated hydraulic mechanisms.
Essential features:
Automated plate feeding systems for precise alignment
Computer-controlled pressure distribution for uniform bending
Real-time monitoring systems for quality control
Heavy-Duty Capacity
Modern plate rolls handle materials ranging from 40mm thick for onshore applications. Offshore wind tower sections often require plates exceeding 80mm in thickness.
Capacity specifications:
Processing plates weighing up to 300 tons per section
Handling steel plates up to 4 meters in width
Achieving tolerances within industry standards
Variable Geometry Options
The latest machines offer adjustable roll positions for different tower section requirements. This flexibility allows manufacturers to create both cylindrical and conical shapes.
Advanced capabilities:
Forming conical shapes with angles up to 8 degrees
Adjustable roll positioning for various diameter requirements
Synchronized support systems for material handling
Quality control measures ensure every component meets stringent industry specifications. Modern manufacturing facilities utilize computerized monitoring systems for consistent results.
The Impact of Efficient Plate Bending on Wind Turbine Manufacturing
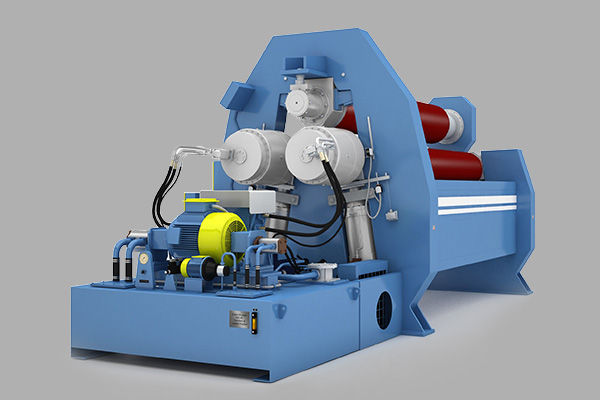
Wind turbine components require sophisticated manufacturing processes to meet industry quality standards. Advanced technology has revolutionized the way tower sections are produced.
Cost Reduction in Manufacturing
Modern sheet bending machine systems minimize material waste through precise control mechanisms. Automated processes reduce labor costs while maintaining consistent quality standards.
Key benefits include:
Lower operational costs through automated material handling systems
Reduced rework requirements due to improved first-pass quality rates
Increased Production Speed and Output
Efficient plate rolling systems contribute significantly to renewable energy production timelines. The latest technology allows manufacturers to process multiple sections simultaneously.
Production advantages:
Completion of tower sections in a quick time
Automated alignment systems reduce setup time between sections
Increased throughput with continuous production capabilities
These manufacturing improvements enable cost-effective wind turbine production at scale. Enhanced efficiency helps meet growing market demands for wind energy components.
Challenges in Plate Bending for Wind Turbines
The fabrication of tower sections demands exceptional precision and specialized equipment capabilities. Modern manufacturing facilities face unique challenges in producing these massive components.
Handling Large-Scale Components
Wind turbine manufacturing requires sophisticated material handling systems for heavy plates. The sheet bending machine must process sections weighing up to 300 tons.
Critical challenges include:
Managing plates over 80mm thick for offshore applications
Maneuvering sections with diameters between 5 to 8 meters
Coordinating synchronized support systems for massive components
Achieving Precise Curvatures and Tolerances
Advanced control systems maintain exact measurements throughout the bending process. Proper alignment ensures consistent quality across all tower sections.
Key technical requirements:
Maintaining conical angles up to 8 degrees
Achieving uniform wall thickness during rolling
Ensuring precise edge alignment for welding
Modern manufacturing systems incorporate automated solutions to address these challenges. Computer-controlled operations help maintain precision during component production.
Wind power technology continues to evolve with increasing demands for sustainable energy solutions. Manufacturing capabilities are expanding to meet these growing industry requirements.
Future of Wind Energy
Wind power technology continues to evolve with increasing demands for sustainable energy solutions. Manufacturing capabilities are expanding to meet these growing industry requirements.
Anticipated Technological Advancements
The future of wind energy drives innovation in plate-bending machine capabilities. Manufacturers are developing systems to handle larger and thicker tower sections.
Key developments include:
Enhanced automation systems for processing heavier materials
Improved precision controls for complex geometrical shapes
Adaptation to Evolving Turbine Designs
Modern manufacturing systems adapt to meet new tower specifications and dimensions. Tower sections are becoming larger to accommodate increased power generation capabilities.
Essential adaptations:
Processing capabilities for sections up to 12 meters in diameter
Systems designed for plates exceeding 140mm in thickness
Renewable Energy Production
Offshore wind installations are driving changes in manufacturing requirements. Production facilities must adapt to create more robust tower components.
Production trends:
Increased capacity for processing monopile foundations
Enhanced capabilities for fabricating hybrid tower designs
Advanced systems for manufacturing floating foundation structures
Modern facilities continue developing new solutions for wind component manufacturing.
Conclusion
Wind power technology continues to evolve with increasing demands for sustainable energy solutions. Modern manufacturing requires specialized equipment to meet these growing industry requirements.
With 40+ years of expertise, Himalaya's plate bending solutions lead the industry. Our machines incorporate advanced automation systems for superior precision control.
Our manufacturing capabilities include:
Twin-speed operation reduces energy consumption by 50%
Special spline-based roll design for maximum efficiency
Crowned rolls compensating for deflection during bending
Himalaya machines deliver exceptional results in wind tower production:
24-hour operational capability with minimal downtime
Comprehensive accessory packages for streamlined manufacturing
Proven track record of over 500 wind towers annually
The robust construction ensures reliable performance in demanding production environments. Our planetary driving system provides efficient processing while maintaining precise tolerances.
Quality control measures are integrated throughout the manufacturing process. Each machine undergoes rigorous testing to ensure consistent performance.
Choose Himalaya for industry-leading wind tower manufacturing solutions. Partner with us to experience the perfect blend of innovation and reliability.
FAQS
Q1. What is a plate bending machine used for?
These machines shape flat metal plates into cylindrical or conical sections. The equipment forms critical components for wind towers using hydraulic roll systems.
Q2. What is the working principle of a roll-bending machine?
The machine uses three or four rolls positioned to apply pressure. Top and bottom rolls grip the plate while side rolls create curvature.
Q3. What is pre-bending in plate rolling?
Pre-bending forms the initial curve at plate edges before full rolling. This process ensures proper alignment and prevents material slippage during production.
Q4. How thick is the steel on a wind turbine?
Plate thickness specifications vary based on tower requirements:
Onshore towers use plates 40-60mm thick
Offshore applications require thicknesses over 80mm
Foundation sections can reach 140mm in thickness
Q5. What challenges are involved in bending plates for offshore wind turbine foundations?
Key challenges in offshore foundation fabrication include:
Processing plates weighing up to 800 tons
Maintaining precise diameters between 5-8 meters
Creating uniform wall thickness in conical sections
Managing material stress during bending operations
Quality control systems monitor each stage of the bending process. Advanced machinery ensures consistent results across all components.
Kommentare