The metal fabrication industry faces significant challenges with plate rolling machines. Safety risks, operational inefficiencies, and maintenance issues often plague these essential tools. According to a report, these challenges become increasingly critical as the market grows, with projections reaching $638.37 Million by 2030.
As experts in the field, we understand business owners and operators' frustrations and concerns. The need for reliable, safe, and efficient plate rolling machines is paramount. We recognize the stress and financial impact of subpar equipment on operations. As one of the leading rolling machine manufacturers in India, we've seen firsthand the industry's struggles.
Himalaya plate rolling machine solutions address these challenges head-on. Our advanced equipment features cutting-edge safety features and user-friendly designs. We prioritize operator safety, machine efficiency, and comprehensive training programs. This blog will explore how the Himalaya enhances productivity and provide peace of mind in plate rolling operations.
Safety Features of Himalaya Machinery Plate Rolling Machines
Safety is paramount in plate rolling operations. Himalaya Machinery integrates advanced features to protect operators and equipment. Let's explore these crucial safety components:
Protective Fuses/MCB and Relay
Himalaya's machines employ independent protection for each motor. Fuses, MCBs, and relays guard against overload conditions. This multi-layered approach ensures robust protection for critical components.
Directional Interlocks
Interlocks prevent reverse movement when rolls are moving forward and vice versa. They also stop upward movement when rolls are traveling downward. These measures minimize the risk of accidents during operation.
Limit Switches
Installed limit switches prevent over-travel in both upward and downward roll movements. This feature protects the machine from mechanical stress and potential damage.
Swing Arm Interlock
A stay-put switch secures the main drive rolling operation when open. This interlock enhances safety by preventing unintended machine activation during maintenance.
Hydraulic Pressure Relief Valve
The hydraulic system includes separate pressure settings for the main and pre-pinching drives. This valve prevents excessive pressure buildup, reducing the risk of component failure.
Mechanical Shear Disc
Electro-mechanical machines feature shear discs to prevent overload in pressure assemblies. These discs protect the machine during upward and downward roll movements.
Key safety features:
Independent motor protection with fuses, MCBs, and relays
Directional interlocks to prevent conflicting roll movements
Limit switches to stop over-travel in roll movements
Hydraulic pressure relief valve with separate settings for different drives
Comprehensive Training for Operators

Himalaya Machinery prioritizes operator proficiency through extensive training programs. These sessions cover all aspects of plate rolling machine operation and maintenance, ensuring safe and efficient use.
Mechanical Assemblies
Operators learn about planetary gearboxes, main cylinders, and roller assemblies. The training covers component functions and their roles in the machine's operation. This knowledge helps operators identify potential issues and perform basic maintenance tasks.
Roller Alignment
Trainees master the art of aligning bottom rollers with top rollers. Proper alignment ensures consistent bending results and reduces wear on components. Operators practice using alignment tools and interpreting measurement readings.
Synchronization System
The program delves into the intricacies of the synchronization system. Operators learn to adjust settings and understand various system functions. This knowledge is crucial for achieving precise and uniform bending results.
Hydraulic Components
Training covers the hydraulic circuit and its components in detail. Operators study main cylinders, swing arm cylinders, and various valves. Understanding hydraulic systems helps in troubleshooting and maintaining optimal machine performance.
Bending Trial
Practical sessions focus on bending shells and cones. Operators learn techniques for achieving different shapes and curves. They practice adjusting machine parameters to meet specific bending requirements.
Electrical Components
The training explores electrical circuit diagrams and component functions. Operators gain insight into control systems and safety interlocks. This knowledge aids in identifying electrical faults and performing basic repairs.
Maintenance and Fault Finding
Trainees learn preventive maintenance practices and troubleshooting techniques. The program covers common electrical and hydraulic issues. Operators practice diagnosing problems and implementing appropriate solutions.
Key training aspects:
Hands-on practice with machine components and controls
Focus on safety procedures throughout all operational stages
Troubleshooting exercises for common machine issues
International Client Service
Himalaya Machinery extends its support globally, as evidenced by a recent case. A PMN/25/E machine, originally sold in India, was transferred to Oman. The company swiftly addressed synchronizer assembly issues and wiring problems. A technician resolved these complications within two days, demonstrating Himalaya's commitment to international client satisfaction.
Common Issues and Himalaya Machinery's Solutions
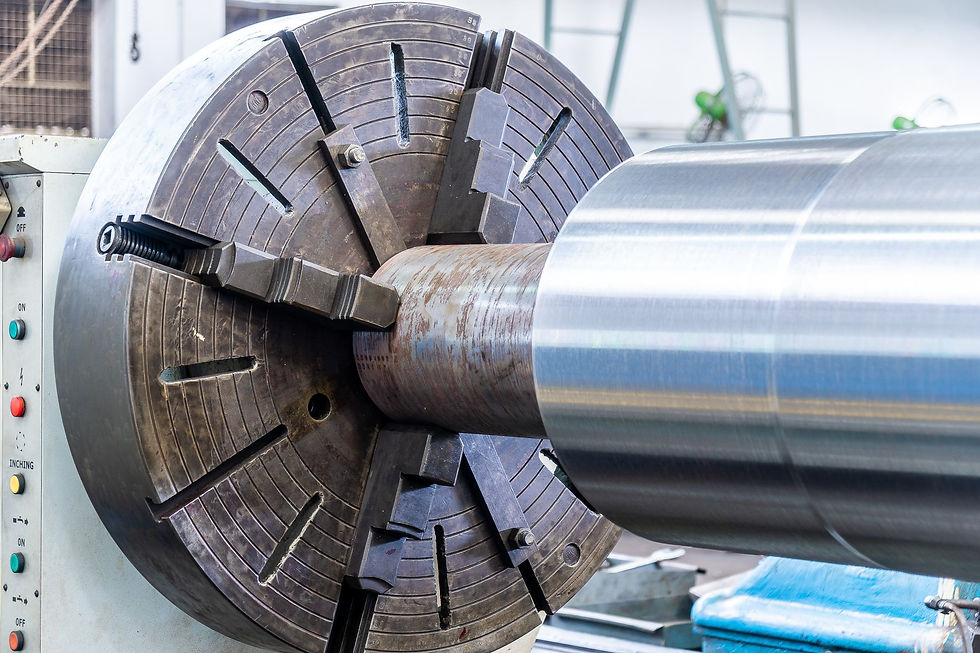
Plate rolling machines face several common challenges, but Himalaya Machinery has developed innovative solutions to address these issues effectively.
Frame Strength
Welding stress and poor load distribution often plague plate rolling machines. These problems can lead to premature wear and structural failures. Common plate rolling machine issues include frame weakness and reducing overall machine lifespan.
Bottom Roll Durability
High torque frequently causes bottom roll breakage in many machines. This issue results in costly downtime and repairs for businesses. Manufacturers must address this vulnerability to ensure long-term operational efficiency.
Synchronizer Assembly
Complex synchronizer assemblies pose maintenance and operational challenges. Operators struggle with intricate systems, leading to potential misalignments and errors. Simplified designs are crucial for improving machine usability and productivity.
After-Sales Service
Inconsistent support quality frustrates many plate rolling machine users. Delayed responses and inadequate technical assistance hinder operations. Manufacturers must prioritize responsive and knowledgeable after-sales support.
How does Himalaya Machinery differentiate?
Robust Frames
Himalaya employs interlocking frames to minimize welding stress and distribute loads evenly. This design enhances overall machine durability and structural integrity. The result is a longer-lasting, more reliable plate rolling machine.
Durable Rolls
Splined designs in bottom rolls prevent breakage due to high torque. This innovation significantly increases the lifespan of critical components. Himalaya's approach reduces maintenance needs and improves operational continuity.
User-Friendly Synchronizer
The synchronizer assembly is designed for ease of maintenance and operation. Operators can quickly learn and efficiently manage the synchronization process. This user-centric design enhances productivity and reduces errors.
Excellent After-Sales Support
Himalaya's after-sales service stands out with the following:
Responsive technical support team available round the clock
Quick issue resolution, often within 48 hours
Comprehensive training programs for operators and maintenance staff
Safety Precautions and Best Practices
Operators must wear appropriate personal protective equipment during machine operation. Regular maintenance checks help identify potential hazards before they become serious issues. Proper training ensures that all staff understand and follow rolling machine safety precautions.
Clear communication protocols should be established for shift changes and emergencies. Keeping the work area clean and free of obstacles reduces accident risks.
Key safety practices:
Perform daily machine inspections before starting work
Never bypass or disable safety features on the plate rolling machine
Implement a lockout/tagout procedure for maintenance and repairs
Ensure all operators are fully trained on emergency shutdown procedures
Conclusion
At Himalaya Machinery, we prioritize safety in plate rolling operations as crucial for business success. Our Himalaya features set new industry standards for operator protection and efficiency. These innovations demonstrate our commitment to addressing real-world manufacturing challenges.
We ensure businesses benefit from reduced downtime, improved productivity, and enhanced worker safety. Our comprehensive training programs enable operators to maximize the potential of our advanced machines.
Key takeaways:
Our advanced safety features prevent common accidents and equipment failures
Our user-friendly designs increase operational efficiency and reduce learning curves
Our responsive after-sales support minimizes disruptions and maximizes machine uptime
Among rolling machine manufacturers in India, we stand out for our holistic approach. Our solutions combine cutting-edge technology with practical industry insights, reflecting our deep understanding of client needs.
Comments