Plate Rolling Machines vs. Sheet Rolling Machines: Key Differences Explained
- Rohan Shah
- Jan 22
- 6 min read
Metal forming processes demand precision and efficiency in manufacturing operations today. Industries face challenges in selecting appropriate machines for their metal bending requirements.
As experts in metal fabrication, we understand the confusion manufacturers face. Choosing between a plate rolling machine and sheet rolling equipment impacts production quality. Production managers often struggle to identify the right machine type.
The right machine selection ensures optimal manufacturing output and cost efficiency. This comprehensive guide explores the key differences between plate and sheet rolling machines. We will examine their design, capabilities, applications, and essential features.
This comparison will help manufacturers make informed decisions for their operations. First, let's start with the basics.
What is a Plate Rolling Machine?
The plate rolling machines bend thick metal plates into various cylindrical or conical shapes. Industries need these machines to create massive storage tanks and pressure vessels.
A plate rolling machine manufacturer designs equipment to handle thick plates. The machine contains three or four rollers that apply pressure to shape metal.
Key features include:
Hydraulic systems enable precise control over bending forces during metal forming
Digital controls help operators maintain accuracy throughout the rolling process
Heavy-duty rollers can withstand extreme pressures while shaping thick plates
Advanced safety mechanisms protect workers during metal plate manipulation
These machines form the backbone of heavy metal fabrication in the construction industry.
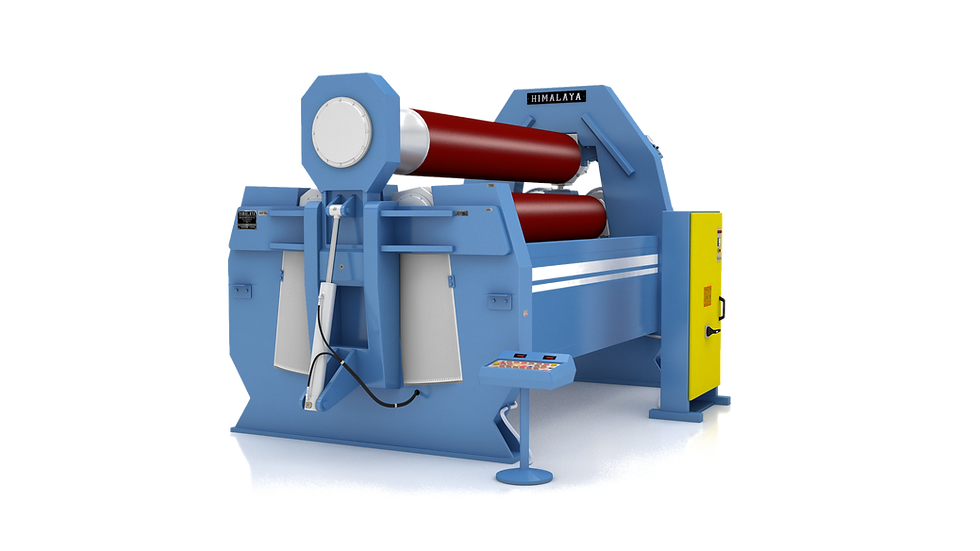
What is a Sheet Metal Rolling Machine?
The sheet rolling machines transform thin metal sheets into curved shapes for various applications. The equipment processes thin metal sheets.
Modern sheet metal rolling equipment features precision controls for consistent bending operations. A sheet metal rolling machine can create cylindrical forms for ducts and decorative elements.
Key features include:
Adjustable roller gaps ensure uniform pressure across the sheet width
Electronic displays provide real-time feedback during the rolling process
Compact design allows for easy workshop placement and mobility
Multiple roller configurations accommodate different sheet metal thicknesses
The versatile sheet rolling process serves both industrial and architectural metal fabrication needs.
Key Differences Between Plate Rolling Machine and Sheet Rolling Machine
Metal fabricators must understand the distinctions between plate and sheet rolling machines. Both machines serve unique purposes in metal forming and shaping applications. Here are the key differences between plate-rolling machines and sheet-rolling machines.
Material Thickness and Capacity
Thickness capabilities create the fundamental distinction between these two metal-forming machines. Metal fabrication shops choose equipment based on their material processing requirements.
A plate rolling machine processes thick, heavy-gauge metal plates for industrial applications. The sheet metal rolling equipment handles thin, lightweight materials for versatile fabrication.
Key differences include:
Plate rollers support materials with substantial thickness for heavy industry work
Sheet rollers excel at the precise bending of thin gauge metals
Plate machines handle wider workpieces with a greater weight capacity
Sheet equipment offers more control for delicate material manipulation
These distinct capabilities determine their applications across various industries.
Machine Design and Construction
Structural differences define the capabilities of metal rolling machines in fabrication shops. The design elements reflect specific requirements for handling different metal thicknesses.
The plate rolling machine features robust frames and large-diameter rollers for stability. A sheet metal rolling machine incorporates smaller components focused on precision control.
Key features include:
Heavy-duty bearings support massive loads in plate rolling operations
Compact roller arrangements ensure accurate bending in sheet processing
Reinforced frames provide stability during heavy plate manipulation
Sheet machines utilize lighter components for enhanced maneuverability
These design variations optimize each machine for specific metal-forming tasks.

Roll Configuration and Design
Roll configurations significantly impact the metal-forming capabilities of these industrial machines. Sheet rolling machines typically feature three slim rollers for precise control.
Every plate rolling machine manufacturer designs robust systems with massive rollers for heavy plates. Sheet rollers use smaller diameter rolls with adjustable pinch points.
Key features include:
Plate machines use three-roll pyramid or four-roll configurations for power
Sheet rollers employ parallel roll arrangements for a consistent surface finish
Plate roller spacing accommodates thick materials with minimal deflection
Sheet machines offer closer roller gaps for handling thin materials
These distinct roller systems determine the quality of finished metal products.
Force and Power Requirements
Power requirements differ greatly between plate and sheet rolling operations. These two factors determine the efficiency of a machine. Modern machines use various drive systems based on material thickness needs.
Advanced metal forming solutions demand high-power hydraulics for plate rolling processes. Sheet rolling machines operate with smaller motors and precise electronic controls.
Key differences include:
Plate rollers utilize powerful hydraulic systems exceeding several hundred horsepower
Sheet machines function efficiently with standard industrial power supplies
Plate rolling requires massive torque to bend thick materials
Sheet rolling focuses on consistent power delivery for uniform results
These power variations reflect each machine's specialized forming capabilities.
Control Systems and Automation
Control systems vary significantly between plate and sheet rolling equipment designs. Modern machines incorporate digital interfaces for precise operation and monitoring.
Each plate rolling machine manufacturer integrates specialized controls for heavy-duty applications. Sheet rolling systems feature more automated functions for repetitive operations.
Key differences include:
Plate machines emphasize manual control options for complex forming tasks
Sheet rollers offer programmable settings for batch production runs
Plate systems provide real-time feedback for critical pressure adjustments
Sheet controls enable quick parameter changes between different material types
These control features enhance operational efficiency across metal forming applications.
Applications and Industries
Different industries rely on metal-forming solutions based on their manufacturing requirements. Both plate and sheet rolling machines serve unique purposes in metal fabrication. Here are the diverse applications and industries where these machines excel.
Plate Rolling Applications
Heavy industries utilize plate rolling for creating large-scale cylindrical and conical structures. These machines shape thick metal plates into components for industrial infrastructure.
The rolling process transforms flat plates into tanks and pressure vessels. Major industries depend on these machines for manufacturing critical equipment components.
Key applications include:
Storage tanks and pressure vessels for petrochemical facilities
Wind tower sections for renewable energy installations
Large-diameter pipes for oil and gas transportation
Heavy-duty structural components for construction projects
These applications demonstrate the vital role of plate rolling in industry.
Sheet Metal Rolling Uses
Sheet rolling enables the creation of various metal shapes for commercial applications. Fabricators produce essential components for everyday products and architectural elements.
Manufacturers rely on sheet rolling for ventilation systems and decorative metalwork. The versatility of sheet rolling makes it essential for diverse industries.
Key applications include:
HVAC ductwork and ventilation system components for buildings
Decorative metal panels for architectural facades and interior design
Rain gutters and downspouts for residential construction
Metal drums and containers for commercial storage needs
These applications showcase the versatility of sheet metal rolling processes.
Conclusion
Understanding the distinct capabilities of rolling machines ensures optimal manufacturing outcomes. Modern metal forming solutions continue to advance with technological improvements.
Himalaya Machinery, with over 40 years of expertise, leads plate-bending machine manufacturing. Their manufacturing complex in Vadodara serves global industries with premium equipment.
Here's a comprehensive summary of the key differences between plate and sheet rolling machines:
Feature | Plate Rolling Machines | Sheet Rolling Machines |
Material Thickness | Heavy metal plates | Thin metal sheets |
Machine Construction | Robust, heavy-duty frame | Compact, lighter frame |
Roller Design | Large-diameter, heavy rollers | Small diameter, precise rollers |
Power System | High-power hydraulic systems | Standard motor drives |
Control Features | Basic controls for heavy forming | Advanced digital controls |
Applications | Storage tanks, wind towers, vessels | HVAC ducts, panels, gutters |
Operation Speed | Slower, focused on power | Faster, focused on precision |
Workspace Requirements | Large, permanent installation | Smaller, semi-portable |
Typical Industries | Heavy manufacturing, petrochemical | Commercial, architectural |
Material Handling | Crane systems required | Manual or light assist is possible |
Frequently Asked Questions
Q: What are the different types of rolling machines?
A: Rolling machines primarily fall into two categories: plate rolling machines for thick materials and sheet rolling machines for thin metals. These machines serve different industrial purposes based on material thickness requirements.
Q: What are the different types of plate rollers?
A: Plate rollers come in three main configurations: three-roll, four-roll, and variable geometry systems. Three-roll machines offer basic bending, while four-roll systems provide enhanced control. Variable geometry machines allow for complex shape forming.
Q: What is a sheet metal rolling machine?
A: Sheet metal rolling machines are specialized equipment designed for bending thin metal sheets. They feature smaller rollers and precise controls for creating curved shapes in lightweight materials.
Q: What are the key differences between plate and sheet rolling machines?
A: The main differences lie in material thickness capacity, machine construction, and applications. Plate rollers handle thick materials for industrial vessels, while sheet rollers process thin metals for commercial products like ducts and panels.
Comments