Metal forming technology has transformed modern manufacturing and construction landscapes. Industries struggle daily to choose the right equipment for their bending operations.
The decision between a plate bending machine and a press brake machine significantly impacts production efficiency and product quality. As industry experts, we understand the challenges manufacturers face when selecting metal-forming equipment, particularly regarding cost implications and operational complexity.
Companies often grapple with balancing initial investments against long-term productivity gains. This comprehensive guide will explore key differences between these bending technologies, comparing their capabilities, applications, advantages, and limitations to help make informed equipment decisions.
Detailed Differences
Manufacturing processes require careful consideration when choosing between different metal-forming equipment. Each technology brings unique capabilities and limitations to metal-bending operations. Here are the detailed differences between plate bending machines and press brakes that matter most.
Material Thickness Handling
A metal bending machine handles thicker plates with robust power systems. The rolling of plates offers flexibility across medium thicknesses, while press brakes excel with thinner materials.
Key thickness handling differences:
Press brakes perform best with thinner materials, offering precise control
Plate rolls manage thicker materials requiring continuous curved formations
Understanding these thickness capabilities helps match the right machine to production requirements.
Bending Accuracy
The hydraulic press brake achieves superior accuracy through controlled downward force and digital positioning. In contrast, plate rolls require multiple passes to reach desired angles, affecting precision.
Key accuracy differences:
Press brakes deliver accuracy within fractions of a millimeter for consistent bends
Plate rollers need operator skill adjustments between passes for precision
Manufacturers must weigh these accuracy factors when selecting equipment for their applications.

Speed and Cycle Time
Production speed creates significant differences between these two metal forming technologies. Each machine type follows distinct operational cycles impacting overall manufacturing efficiency.
Key speed differences:
Press brakes complete single bends swiftly but require multiple setups
Plate rolls process continuous curves in one pass with minimal adjustments
The choice between technologies impacts production schedules and delivery timelines.
Cost Comparison
Cost considerations extend beyond initial equipment purchases into long-term operational expenses. Most plate-bending machine manufacturers offer diverse pricing options based on automation levels.
Operating costs vary between technologies, with power consumption playing a significant role. Maintenance requirements affect the total ownership cost throughout the equipment's service life.
Key cost factors:
Press brakes demand higher initial investment but lower operating expenses
Plate rolls require specialized maintenance skills and periodic roller replacements
Regular preventive maintenance programs help optimize equipment performance and longevity.
Operating Space Requirements
Space utilization differs significantly between metal-forming equipment types in manufacturing facilities. The metal bending machine requires additional clearance for material handling and operational safety.
Workshop layout planning must account for material movement and operator access zones. Each technology presents unique spatial challenges for optimal production flow.
Space considerations:
Press brakes need front and rear clearance for material manipulation
Plate rolls demand extended space for long material-feeding processes
Efficient space planning ensures smooth material flow and safe operating conditions.
Plate Bending Machine: Types
Understanding different types of plate-bending machines helps optimize metal-forming operations. Each variant brings specific advantages to handle diverse manufacturing requirements. Here are the main types of plate-bending machines that shape modern metalworking processes.
Three-roll plate benders
Each plate bender type brings unique advantages to metal forming operations. The metal bending machine configurations adapt to diverse manufacturing needs.
Traditional design provides reliable performance for standard cylindrical and conical shapes.
Side roll adjustments enable precise control over bending radius parameters.
Four-roll plate benders
Advanced technology enhances production efficiency through innovative roll configurations and controls.
Double pinch design reduces material handling and operator intervention
Pre-bending capabilities eliminate flat spots at plate ends effectively
Variable geometry plate benders
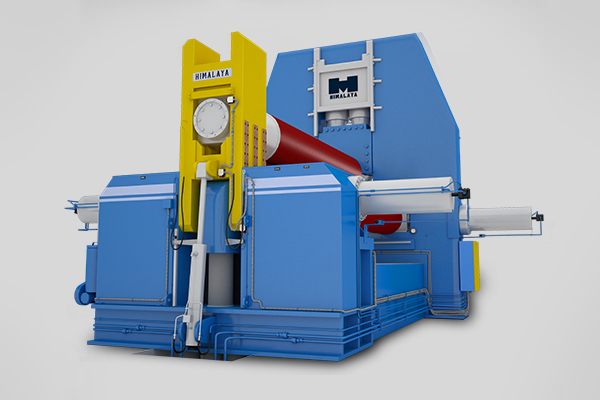
Modern designs offer flexibility through adjustable positioning and programmable settings.
Adjustable roll positions accommodate complex shape formations with minimal passes.
Programmable configurations adapt to different material thicknesses and diameters.
These distinct features help manufacturers select equipment that matches their production requirements.
Summarized table
Here's a concise comparison table of the key differences:
Feature | Press Brakes | Plate Bending Machines |
Bending Type | Angular/V-bends | Curved/Cylindrical bends |
Material Thickness | Best for thin to medium | Handles medium to thick |
Accuracy | High precision for angles | Moderate for curved surfaces |
Speed | Fast for single bends | Slower, requires multiple passes |
Space Required | Compact footprint | Larger floor space needed |
Initial Cost | Higher initial investment | Moderate initial cost |
Operating Cost | Lower power consumption | Higher power requirements |
Best For | Sheet metal, panels, brackets | Pipes, tanks, cylinders |
Operator Skill | High skill required | Moderate skill needed |
Maintenance | Regular tooling maintenance | Periodic roller maintenance |
Plate Bending Machines Uses
Metal forming equipment serves diverse industries with specialized bending requirements. While press brakes focus on angular bends, plate bending machines offer different capabilities. Here are the primary applications where plate-bending machines excel in industrial settings.
Metal forming applications span across multiple industries requiring curved and cylindrical shapes. The plate-bending machine transforms flat metal sheets into various curved configurations.
These machines excel in heavy industrial manufacturing, where large-scale components need precise curves.
Key applications include:
Creating large storage tanks and pressure vessels for industrial facilities
Forming wind tower sections and heavy equipment components
Manufacturing industrial piping systems and structural supports
Industrial manufacturers rely on these machines for consistent curve formation in components.
Press Brake: Types
Modern manufacturing utilizes various press brake technologies for metal forming operations. The press brake machine selection impacts production quality and operational efficiency.
Hydraulic press brake
Advanced hydraulic systems provide consistent force distribution across bending lengths.
Programmable pressure controls enable precise adjustments for different material thicknesses.
Mechanical press brakes
Direct drive systems deliver high-speed operation for repetitive bending tasks.
Robust mechanical components ensure reliability in demanding production environments.
Servo-electric press brakes
Energy-efficient motors maintain precise position control during bending operations.
Digital servo systems enable complex bend sequences with minimal setup time.
These features guide manufacturers toward equipment that matches their specific requirements.
Press Brake Uses
Metal fabrication industries rely on versatile equipment for precise angular bending operations. Press brake uses span across multiple manufacturing sectors, meeting diverse production requirements. Here are the key applications where press brakes demonstrate their essential capabilities.
Manufacturing sectors depend heavily on precision bending for diverse product applications. Unlike a plate bending machine, the press brake machine specializes in angular formations.
The hydraulic press brake delivers consistent results across various material types. Modern press brake uses extend from small components to large industrial products.
Key manufacturing applications include:
Creating enclosures and cabinets for electronics and telecommunications equipment
Forming structural components for construction and architectural elements
Producing brackets, frames, and panels for automotive and aerospace industries
These versatile machines transform metal sheets into essential components for multiple sectors.
Conclusion
Selecting the right metal forming equipment requires careful evaluation of production requirements. Having more than 40 years of experience, Himalaya Machinery has become India's reliable producer.
Leading plate-bending machine producers such as Himalaya Machinery provide specific solutions for different uses. Our extensive manufacturing facility in Vadodara serves global metal forming needs.
Key selection factors to consider:
Material thickness requirements determine the most suitable bending technology
Production volume and speed needs influence equipment choice significantly
Space constraints and cost considerations shape the final investment decision
Understanding these factors helps manufacturers make informed decisions for their operations.
Frequently Asked Questions
Q: Is a panel bender better than a press brake?
A: Panel benders excel at complex panel formations, while press brakes offer versatility across simpler bending operations. Each serves different manufacturing needs based on production volume and part complexity.
Q: What is the difference between a folding machine and a press brake?
Press brakes apply downward force; folding machines make bends using upward-moving beams. Though they need more floor area, folding machines handle larger panels with less marking.
Q: Which is better - mechanical press brake or hydraulic press brake?
A hydraulic press brake provides better control and accuracy for varied materials. For high-volume, repetitious jobs, mechanical press brakes offer speedier operation.
Q: What are the disadvantages of press brakes?
A: Press brakes require longer setup times for complex bend sequences. They face material thickness restrictions based on machine capacity. Multiple operations are often needed for complex shapes. High operator skill levels are necessary to achieve precise results.
תגובות