Metal Plate Rolling Machines: Working, Intricacies & Functionalities
- Rohan Shah
- Jun 2, 2023
- 7 min read
Updated: Oct 18, 2023
Have you ever wondered how these huge tanks and machines are built? In childhood, I thought they just melted iron or metal and let it dry. Little did I know about the concept of metal plate rolling machines.
Metal plate rolling machines give the conical and cylindrical shapes or bend the metal plates at required angles. This is how workshops worldwide utilize metal plate rolling machines for manufacturing.
We know what you are thinking. “How does that happen? Sheets are fine, but how do you roll or bend a metal plate?” It’s due to the malleability and ductile strength of metal plates.
Malleability is a metal’s ability to be formed into sheets. Ductile strength is how much pressure a metal plate can take to be rolled and not break.
But how does it work?
How does the machine roll these thick and hard metal plates?
We will answer all the questions making circles in your mind. However, to understand how a plate rolling machine works, let’s first understand what functions different parts of a plate rolling machine serve.
In-Depth Look at Different Parts of a Plate Rolling Machine
These machines are extremely heavy-duty, and their build is as solid. Every part of these machines plays an important role in plate rolling.
Let’s explore what these 20 parts of a plate rolling machine do:
1) Frame - It is the body of a plate rolling machine. Provides stability and structural support.
2) Upper Roll - Upper roll is mostly an idler. It rotates at its place and doesn’t move up, down or toward sides.
3) Bottom Rolls - They move up, down, and sideways to adjust the metal plate and roll it at a desired angle to form a cylinder, cone, or arc.
4) Side Rolls - Side rolls support metal plates to maintain uniform rolling.
5) Support Rolls - Same as side rolls, they provide support for metal plates.
6) Drive System - Transfers power from the hydraulic system to rolls for rotation and movement.
7) Control Panel - All the rotational, pressure and other machine controls are housed here.
8) Hydraulic System - Powers roll movements and control precision in plate rolling.
9) Guide Rolls - Makes sure the alignment of a metal plate is accurate while passing through rolls
10) Pinch Rolls - Their dedicated function is to feed the plate into the machine.
11) Pre-Bending Rolls - Utilized for pre-bending on the plate edges.
12) Anti-Deflection System - Negates powers causing plate deflection and minimizes deflection during the rolling process.
13) Lateral Guide System - Ensures proper alignment of the metal plate
14) Clamping System - It holds the metal plate firm while the rolling job is underway.
15) Digital Display - DRO (Digital Readout) displays measurements and settings of different pressure and motor systems. Also helps in repeating a job if the reading are pre-recorder.
16) Lubrication System - To reduce wear and tear, the lubrication system keeps rolls, motors, and other parts prone to depreciation lubricated.
17) Cooling System - Cools down hydraulic oil, which is getting circulated between the hydraulic power pack and all hydraulic cylinders/hydro motors.
18) Material Handling System - Makes it easier to load and unload metal plates to and from the machine.
19) Tilting Table - Helps feed metal plates at a fixed angle. Largely used for heavy/thick metal plates.
20) Conveyors - Makes it easier to feed longer metal plates to the plate rolling machines.
For some parts of these machines, you would think they do the same thing. However, the case is this machine does only one work, i.e., rolling metal plates. So many parts only coordinate and perform this function to achieve near-perfect accuracy for rolled metal plates.
Moving forward to how a plate-bending machine works.
Working Mechanism of a Plate Rolling Machine: Explained!
The number of rolls in a plate rolling machine varies depending on the requirements of a workshop. Generally, there are either 3 or 4 rolls in plate rolling machines. It is because these machines roll metal plates of thicknesses that are required in most applications.
There have also been 5, 6, 7, and even 8 rolls in a single plate rolling machine! It is to be noted that the requirement for these types of machines is scarce. They are only custom-made due to a lack of buyers. 3 and 4 roll plate rolling machines are the most commonly used machines. Therefore, today we will understand the working of 3 and 4-roll plate rolling machines.
Part 1 - How Does a 3-Roll Plate Rolling Machine Work?
A 3-roll plate rolling machine is your go-to choice for rolling thin metal plates up to 3-4 inches. It provides precision and is more cost-effective than a 4-roll plate rolling machine. The only thing to remember is the thickness of the plate you want to roll.
You need to perform three steps while rolling a metal plate on a 3-roll plate rolling machine.
Pre-bending
Center alignment
Roundness correction.
An operator will obtain the metal plates and check for defects. It is important to do so to steer clear of failed rolling attempts in the future. They will also check for material quality and specifications to be at par with national or international standards.
The operator will turn on the machine after checking the lubrication system. They will derive the machine's status by observing the rolls and the pressure by looking at a Digital Readout. The machine is now ready for pre-bending.
Step 1: Pre-Bending on 3-Roll Plate Rolling Machine
The side rolls are placed closer, and a metal plate is fed to the machine to receive the initial bend. Now the machine is turned on to commence the metal plate rolling process.
The top roll exerts pressure on the plate, while the side rolls apply pressure to the sides. To achieve the desired curvature, the operator adjusts the angle and placement of the metal plate.
Here’s an image to understand how pre-bending shapes the tail and edge of a metal plate.

Step 2: Center Alignment on a 3-Roll Plate Rolling Machine
Upon the completion of pre-bending, it is now time to align the metal plate in the center so that the power is distributed uniformly throughout the surface.
The operator will now adjust the side rolls to put the plate firmly. Next, they will check alignment and fine-tune adjustments.
Once the operator is satisfied with the center-aligning of the plate, they will secure it in place using the clamp system.
Step 3: The Real Rolling Process
Pressure and rotation parameters are now set, and the plate is in place. Next, the operator lets the plate pass through the rolls.
Both the bottom rolls will drive the pressure to the plate. The speed of rotation and pressure in both bottom rolls are different. It results in the metal plate bending or rolling at the desired angle.
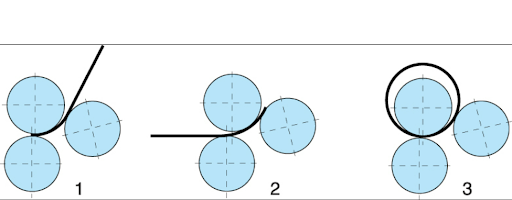
Step 4: After-Rolling Roundness Correction
The metal plate might have some deflection. They check if a perfect cylindrical or an arc is forming. If it isn’t, there is a need for roundness correction. The operator now asks the laborers to make sure both ends meet correctly.
Let’s move to the working of the 4-roll plate bending machine.
Part 2 - How Does a 4-Roll Plate Rolling Machine Work?
The most beneficial thing about 4-roll plate rolling machines is that they give the desired results within a single feed. It means that a workshop can get its rolling job done in half the time compared to a 3-roll plate rolling machine, which has to be fed twice for pre and post-bending and rolling.
There are three bottom rolls and a top roll. More bottom rolls result in better accuracy and precision throughout the rolling procedure.
Once the operator has obtained the metal plate, they will check for the material, its ductile strength, and malleability. After confirming that the metal plate meets national or international standards (according to where the machine will be used), they will set the diameter, pressure, and rotational parameters for the metal plate.
The Single-Step Rolling Process
Pre-bending, rolling, and post-bending are all done in a single feed. The operator inserts the metal plate between the top and bottom rollers.
Pre-pinching is done upon the metal plate entering the machine. Then it rolls into a desired cylindrical or conical shape.
Once the rolling process is complete, the metal plate gets post-bent, ending the process of rolling.
It is necessary to understand that both these machines can roll the same thickness of metal plates (a 4-roll plate rolling machine can also roll thicker ones with better precision), but 4-roll cousins are beneficial as they save half the time.
A 3-roll plate rolling machine would be a good choice if one is tight on their budget. Otherwise, there is no better investment than a 4-roll plate rolling machine. Talking about investments. It is necessary to perform maintenance of your machine. The machine manual will have the directions for maintenance. But we have some tips for you to keep your plate rolling machine’s efficiency at its best.
Quick Maintenance Tips for Plate Rolling Machines
Follow these 6 essential tips for machine maintenance.
1) Inspecting the plate rolling machine - Check the bearings, gears, rollers, frame, hydraulic systems, and other parts of the machine.
2) Take precautionary protocols for machine maintenance - Don’t use solvents or inflammable materials, and make sure grease doesn’t disperse in the air.
3) Perform detailed inspection before rolling the metal plate - Check if external parts, indicator lights, and the pressure gauge are working properly. Also, check for leakage in tubes and pipes.
4) Perform weekly maintenance of the plate rolling machine.
5) Perform monthly maintenance of the machine.
6) Annual maintenance is extremely important as you need to check if any part needs replacement.
You can also read our informative article “A Complete 6-Step Guide to Maintenance of Plate Rolling Machine” to learn more about machine maintenance.
To Conclude
Plate rolling machine is a highly mechanical equipment. You must know which machine your workshop requires to make the most out of it. While a 3-roll machine is cheaper, a 4-roll plate rolling machine will double the productivity. Your choice can always depend on your priority needs.
We hope this article has helped you with questions in your mind. Feel free to ask any questions and contact us, Himalaya Machinery, if you have a plate rolling machine requirement.
Comments