It is basic human nature to learn most from their mistakes. Yet, there are always ways to learn firsthand and avoid larger mishaps. Plate bending is an industry where you cannot afford to have mistakes from even the simplest of margins. Hence, it becomes extremely important to nullify any possibility of mistakes that you know may happen.
The plate bending industry provides machinery and equipment solutions for almost all the mainstream industries such as shipping, metal fabrication, windmill manufacturing, earth moving, metal structures, oil tanks, silos and several others. Mis-bent metal plates may sometimes go to waste since there is not always a scope of after-work on the bent or rolled metal plate.
Many workshops try and overload the machines, which causes the machine to lose their longevity. If the rolls are not crowned, they may create a problem, and even when they are crowned, there is always a worry if the roll being crowned too much or too little.
Yet, the mistakes are not limited to what we just shared. There are more, and we would like to share them with you today. Let’s discuss seven very common mistakes made in the plate bending or plate bending industry.
7 Common Mistakes of Plate Bending Industry
The first mistake that we will be discussing is a non-technical, yet the one that needs to be addressed right away if you are making it. The other six are technical mistakes and can possibly be addressed really well if you kick off the first mistake out of the scenario.
Following are the seven mistakes that we will be discussing in this article:
Unskilled workforce
Miscalculated minimum bending radius
Uneven bending
Wrong selection of roll for bending job
Workpiece surface damage due to no initial measures
Rolls that are not crowned
Metal plates that are not levelled and unshoveled welds
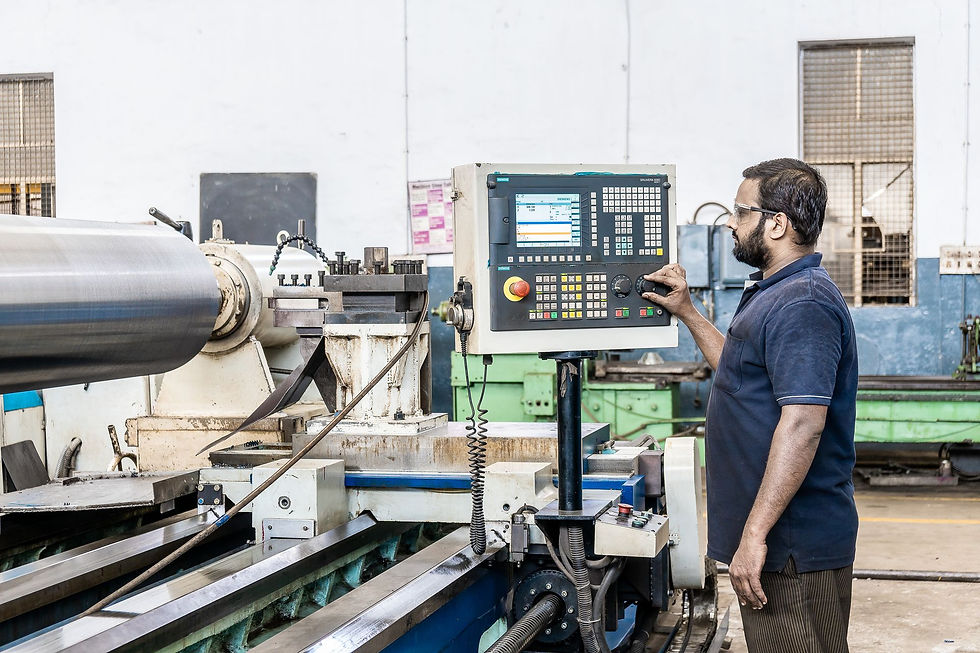
1) Unskilled Workforce
While running a workshop, an unskilled workforce is the last thing you need in your arsenal. Hire a skilled workforce to make sure that your machinery and the workshop itself are in more knowledgeable and expert hands. It is only beneficial to either have a skilled workforce or train your workforce and make your workers skilled enough to let your workshop function at its possible best in all conditions
2) Miscalculated Minimum Bending Roll Radius
As discussed above, a skilled worker can make a difference in the productivity of your workshop. A too-tight radius for your workpiece, i.e., the metal plate, will not only result in the mis-bent metal plate but will also create the possibility of inaccurate results in the final product. Also, there is a chance of the equipment getting broken, which is not advised since the plate bending machines are a big investment.
3) Uneven Bending
What use is a rolled metal plate the way you don’t want it? Uneven bending is never welcome in the workshops since no one wants inefficient and low-quality work for their equipment and workpiece. There is natural uneven bending, but that is of accepted standards. Uneven bending that largely comes due to poor roll and machine maintenance is something that is unwelcome.
4) Wrong Selection of Roll for Bending Job
Polished, hard-chrome plated, precision-ground and other types of rolls are available for various industries that use metal plate bending machines. In order to get the nearly ideal output that you want, you must make the best choice regarding the type of roll that will be used to perform the bending process of your metal plate.
5) Workpiece Surface Damage Due to No Initial Measures
Wrong roll type, too much or too less pressure, uneven bending, miscalculated radius, and various other factors may damage the workpiece. Moreover, the metal rollers that are not well maintained might also affect the bending process. Thus, if the initial measures as stated above are not followed, you must prepare for workpiece damage.
6) Rolls that are Not Crowned
As a workshop, it is possible that you will mostly have the same kind of bending work to perform. In such cases, it is advisable to crown the rolls in order to nullify any possibilities of getting irregularities at both tails of the metal plate you are bending. Not crowning the roll will only work against your goals which no workshop wants to happen.
7) Metal Plates that are Not Levelled and Unshoveled Welds
When the metal plate is inserted between the plate rolls, it must be perpendicular to the plate rolls. If the metal plates are not levelled and have unshoveled welds, they will not be perpendicular to the rolls of the bending machine. The directly rolled metal plates will hence have uneven rolling, mis-bent shape and may also break at times.
It is necessary to understand that as a workshop, maintaining your plate bending machine is extremely important. Also, the work that is to be done needs mathematic calculations and a skilled worker who will take care of the process in and out. No amount of post-processing can provide you with what results you can get after taking pre-processing of the bending job. If a workshop knows this, it will perform at its very best.
Final Words
We have discussed it all today. Be it skilled workers or the type of roll that needs to be selected, all the mistakes that we have listed above are the ones people have already made, and we are sure that once you have read this article thoroughly, your workshop will be more productive and more careful towards the maintenance of the plate bending machine. We are Himalaya Machinery, leading providers of plate bending and straightening solutions all over the globe. Contact us for all your plate bending needs or for getting more information.
Bình luận