Metal fabrication defects can result in catastrophic structural failures that undermine safety, project timelines, and your bottom line! Small defects in quality tend to snowball into major issues that result in costly rework and loss of customer relationships.
As experts in the metal fabrication industry, we are fully aware of the tremendous pressure you face when a quality issue arises. Reputation is founded on consistently delivering quality and maintaining quality control processes in metal fabrication, directly influencing customer satisfaction and business sustainability. The stakes are high when component failure could result in liability cases or contract losses.
Systematic quality control is a simple solution to these challenges. With well-established inspection routines and verification systems in place, you can revolutionize production outcomes. Seven basic quality control processes are explained in this blog that will make you a master in metal fabrication works.
Which are the 7 quality control processes essential for metal fabrication?

Established quality processes are the cornerstone of excellence in metal fabrication. Every fabrication shop should have consistent methods in place to ensure high product quality. Let’s explore some of the critical quality control processes that are key to achieving superior results:
1. Project Planning and Design
Project success begins much earlier than when you make that first cut in metal. Your engineering team must determine fabrication parameters. These are planning considerations in quality control.
Create detailed CAD designs with clearly defined tolerances
Perform design reviews with production and engineering teams
Document every engineering change and client requirement
Implement staged design approvals with the signatures of stakeholders
Use simulation software to predict potential fabrication issues
Establish communication protocols between design and production teams
Metal fabrication process planning must include material selection with substitutes, with careful attention. Specifications must be scrutinized by your team for clarity before production. Thorough engineering inspections can detect flaws in advance.
2. Material Inspection and Testing
Material quality directly affects your final product performance and appearance. Your inspection program should verify material properties before production begins. Here are the material inspection requirements for quality assurance.
Ensure that material certifications meet purchasing specifications.
Implement incoming material inspection procedures.
Document all material nonconformances and dispositions.
Train to receive staff in material identification.
Perform random material testing on critical applications.
Guarantee material traceability throughout your production process.
Proper machine setup and adjustment are essential for metal forming. For instance, the plate rolling machine setup directly affects dimension and appearance. Machine operators must follow setup procedures to achieve consistent outcomes.
3. Quality Control Process Definition and Control
Process definition forms the foundation for repeatable quality outcomes. Not only should steps be defined in your procedures, but also acceptance criteria. These are quality assurance process definition requirements.
Document process parameters with acceptable ranges.
Establish visual standards for subjective quality characteristics.
Perform process audits to verify compliance with procedures.
Set quality responsibilities for each production position.
Document inspection frequencies and sampling plans.
Establish standardized forms for data collection on quality.
Workflow optimization eliminates wasted motion and redundant effort in manufacturing. Your metal fabrication workflow must reduce material handling between stages. Optimal workflows reduce opportunities for contamination and damage.
4. Welding Inspection and Testing
Welding quality directly affects structural strength and component performance. Your welding quality program must have both visual and technical inspections. Listed below are welding quality assurance requirements.
Implement welder qualification and certification programs.
Document welding procedures for each material type.
Establish visual weld inspection standards with examples.
Perform periodic destructive testing on weld samples.
Train weld inspectors on weld defect detection.
Perform root cause analysis on weld failures.
Specialized testing staff requires specialized training and certification. Acceptance and rejection levels. Quality control processes must be instituted for weld verification.
Forming operations introduce stress that can affect material integrity. Your bend process monitoring systems should verify proper forming procedures. Material springback varies with thickness and composition, requiring adjustments.
5. Performance and Tolerance Testing
Performance testing ensures that parts will perform as intended. Wherever possible, you should replicate actual conditions of operation in your testing. The performance testing needs for quality assurance are outlined here.
Establish testing procedures specific to component functionality.
Document test results with operator identification.
Set pass/fail criteria for objective measurement.
Utilize proper testing equipment with calibration verification.
Develop reaction plans for test failures.
Maintain records of testing for traceability and analysis.
Dimensional accuracy ensures proper fit and functionality in assemblies. Your metal fabrication quality standards must include measurement protocols. Precise measurement tools are in accordance with component tolerance specifications.
Equipment calibration ensures consistent and reliable manufacturing results. Frequency and technique must be a component of plate rolling machine calibration. Traceable standards allow you to have confidence in measurement accuracy.
6. Documentation and Record Keeping
Documentation is proof of implementation and compliance with a quality system. Thoroughness and retrievability must be balanced in your record system. Here's what you need to ensure quality control for metal fabrication:
Implement document control systems with revision tracking.
Establish standardized forms for collecting data on quality.
Document retention policies that meet industry standards.
Establish backup systems for critical quality records.
Implement electronic signature systems for approvals.
Establish document retrieval systems for audits.
Documentation of quality provides proof of implementation and performance of a system. Your documentation should lay out the whole quality story for each component. Records allow traceability from raw materials through finished goods.
Documentation is both a reference and a training document. Your records need to be retrievable and easy to access when audited. Plate rolling machine manufacturer compliance records demonstrate equipment capability and maintenance.
7. Final Inspection and Delivery
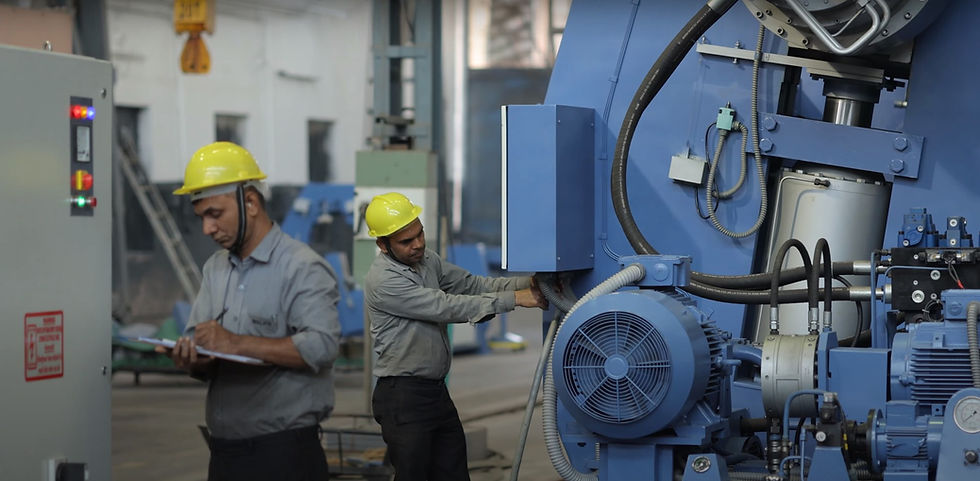
A final inspection is the last quality check before customer delivery. Your final inspection standards must be in line with customer specifications and expectations. The specifications that follow are final inspection specifications for quality assurance.
Design tailored final inspection checklists based on product type.
Document findings along with the inspector’s name.
Set hold points for checking critical characteristics.
Establish cleaning and packaging standards.
Create shipping preparation verification steps.
Set delivery documentation requirements.
Pre-shipment inspections prevent quality escapes and customer dissatisfaction. Both visual and measurement inspections should be a part of your final check. Documentation is evidence of careful inspection before shipment.
Final cleaning ensures positive first impressions with customers at delivery. Your packaging specifications need to be engineered to avert component shipping damage. Metal fabrication industry compliance includes proper documentation with shipments.
What are the Best Metal Fabrication Practices?
Metal fabrication excellence requires both systemic approaches and technical expertise. Your most effective practices need to combine learned experience with industry standards. These are fundamental best practices for superior results in our experience.
1. Quality Standards Implementation
Your standards implementation needs to have a training and verification element. Employee comprehension is what leads to consistent application across production.
The proper process tracking of metal fabrication guarantees adherence to standards and performance. Proactive and reactive elements must be incorporated in your quality system. We recommended regular audits to help keep you in compliance with standards.
Document applicable standards for each product type
Create training materials to ensure compliance with industry standards
Develop internal audit programs based on standards
2. Employee Training and Certification
Employee knowledge directly affects quality and consistent outcomes. Technical skills and quality awareness must be a component of your employee development program. Employee capability is validated by certification.
Skills matrices identify training needs in your organization. In our experience, both on-the-job and formal training need to be included in your program. Continuous knowledge verification sustains capability as needs change.
Create standardized training materials with visual support
Develop skills evaluation for critical functions
Document employee qualifications for particular processes
3. Equipment Maintenance and Calibration
The condition of equipment directly impacts your quality results and consistency. Prevention and production availability should be balanced in your maintenance program. Documentation provides proof of equipment care and capability.
Plate rolling machine manufacturer specifications dictate maintenance requirements and intervals. We recommend that you include operator technical maintenance in your metal fabrication process. Regular calibration checks will enable you to have consistent machine performance over time.
Establish preventive maintenance schedules by equipment type
Document maintenance procedures with essential parts
Set equipment history records for trend analysis
4. Process Automation and Digital Integration
Automation removes variation caused by human actions and decisions. Automate variation-rich or high-risk processes in your automation plan. Electronic systems improve documentation completeness and availability.
Automated systems improve consistency in process verification of quality control. Your digital integration must connect quality data with production data. We have also noticed that real-time monitoring is very helpful in enabling intervention at the point where quality control processes stray.
Determine high-variation processes for priority automation.
Set up digital data collection for quality metrics
Implement automated inspection where technologically feasible
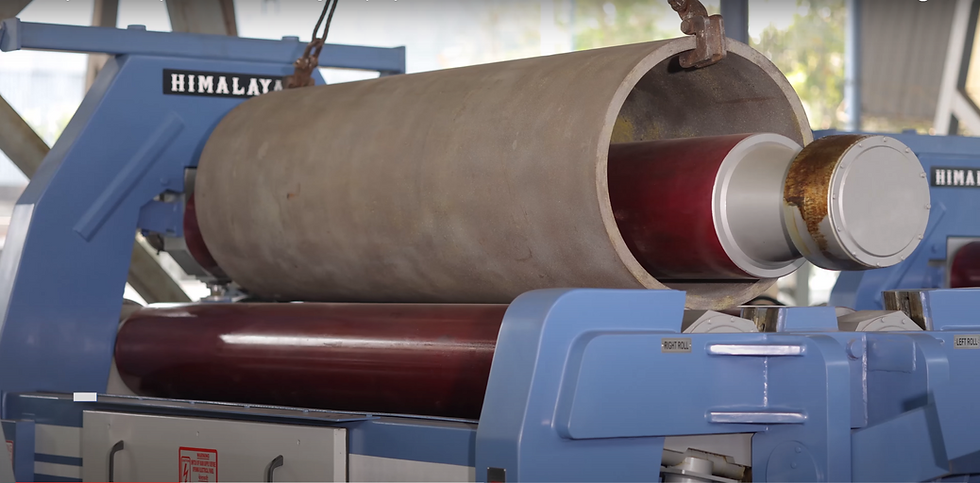
Metal Fabrication Success: Guaranteed!
Quality control processes form the foundation of exceptional metal fabrication operations. Your commitment to quality systems creates consistent results that customers value. Implementing the seven essential processes transforms your manufacturing capabilities and reputation.
The plate rolling machine maintenance standards you establish directly impact product quality. Your equipment care program demonstrates a commitment to manufacturing excellence. Quality begins with reliable, well-maintained equipment and continues through delivery.
At Himalaya Machinery, we have stood as a premier provider of metal fabrication equipment with unmatched quality standards. Our comprehensive support programs ensure your equipment maintains peak performance capabilities. Through unparalleled engineering expertise, we have delivered machines designed for precision and reliability in demanding applications.
FAQs
1. How often should calibration be performed on metal fabrication equipment?
Critical measurement equipment should undergo calibration verification at least quarterly. Production equipment typically requires calibration checks monthly or after maintenance activities. Your calibration frequency should increase when statistical analysis shows measurement drift or after equipment repairs.
2. What documentation should accompany metal fabricated products during delivery?
Typical delivery documentation includes material certifications, dimensional inspection reports, and any required testing results. Special processes like heat treatment or plating require additional certification documentation. Customer-specific requirements may include specific forms or electronic data submission.
3. How can small fabrication shops implement effective quality control?
Small shops should focus first on documentation of processes and inspection requirements. Even simple check sheets create consistency and traceability in operations. Prioritize calibration of measurement tools and employee training for greatest quality impact.
4. What are the most common quality issues in metal fabrication?
Common quality problems include dimensional accuracy, welding defects, and material substitutions. Surface finish issues frequently cause customer rejections despite meeting functional requirements. Documentation gaps represent another common finding during quality audits.
Commentaires